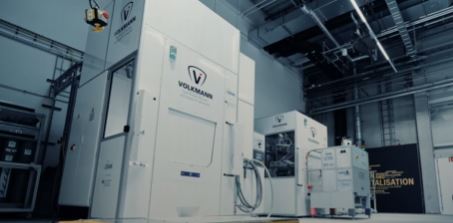
BMW, GKN Additive Manufacturing y Volkmann impulsan la investigación en impresión 3D
Tres lecciones clave aprendidas en la transferencia y recuperación de polvo metálico
Las empresas de impresión 3D y otras que impulsan el auge de la fabricación aditiva han estado invirtiendo discretamente enormes cantidades de recursos en aprender sobre el proceso de impresión 3D y perfeccionarlo para producir piezas metálicas de mejor calidad de forma más eficiente y a menor coste. Varios actores clave de la fabricación aditiva han estado investigando, desarrollando y probando una amplia variedad de materiales y equipos para crear una base de conocimientos sobre las propiedades del polvo metálico, las normas de control de calidad, las directrices de ensayo e inspección de piezas y las mejores prácticas.
El Grupo BMW, fabricante mundial de automóviles, y GKN Additive, la división global de fabricación aditiva de GKN Powder Metallurgy, se han unido a Volkmann y a otras empresas que ofrecen un alto nivel de experiencia en ingeniería en un proyecto único diseñado para crear la tecnología necesaria para hacer avanzar la impresión 3D metálica hasta el punto de poder integrarla en las líneas de producción convencionales y agilizar el proceso de fabricación. Se llama IDAM, «Industrialización y digitalización de la fabricación aditiva (AM) para procesos de series automovilísticas», y lleva en marcha desde el 27 de marzo de 2019.
Cuatro años después, todos hemos aprendido mucho sobre la fabricación de piezas metálicas mediante impresión 3D. Estas son tres de las lecciones clave:
Se ha demostrado que casi todo el proceso de producción de la impresión 3D puede automatizarse de principio a fin. Desde el principio, se había previsto que la estratificación y la construcción de la pieza metálica fueran un proceso automatizado. Pero ahora se sabe que para producir piezas metálicas impresas en 3D de alta calidad de forma constante es necesario automatizar el mayor número posible de pasos auxiliares, a fin de proteger los polvos metálicos de la contaminación y a los trabajadores de la exposición a sustancias tóxicas. Esto implica transferir automáticamente los polvos metálicos desde los contenedores de almacenamiento, eliminar los polvos metálicos no utilizados de la cámara de construcción y realizar tareas de acabado secundarias, como el desbarbado y la limpieza. Se pueden eliminar las tareas manuales, como la manipulación de polvos, que suponen un riesgo tanto para los trabajadores como para los materiales en polvo.
También hemos demostrado que incluso cantidades mínimas de humedad pueden afectar negativamente al polvo metálico y alterar sus propiedades. Esto requiere que se controle cuidadosamente el nivel de humedad en las instalaciones y que los polvos metálicos se mantengan aislados del entorno de la planta durante su almacenamiento y transferencia a la impresora. De lo contrario, las partículas, que antes eran finas, pueden aglomerarse en pequeños grumos que no fluyen bien durante la transferencia y provocan imperfecciones como poros y rebabas si se dejan pasar a la impresora. Para mantener la calidad del polvo metálico incluso en condiciones ambientales cambiantes, Volkmann GmbH ha desarrollado un secador al vacío en línea que elimina automáticamente el exceso de humedad y devuelve los materiales al contenido de humedad correcto. Este sistema de secado de polvo se puede utilizar para secar materiales vírgenes recién llegados del proveedor de polvo metálico y para preparar el material sobrante o no utilizado para su reutilización.
Dado nuestro compromiso con el reciclaje, la reducción de residuos y la eficiencia, estamos muy orgullosos de haber desarrollado la capacidad de extraer automáticamente el material metálico no utilizado de la cámara de construcción, cribarlo para detectar aglomerados, secarlo y devolver los polvos que cumplen las especificaciones al proceso de impresión o al almacenamiento para su reutilización. Incluso estamos mezclando material reciclado y virgen en diferentes proporciones, dependiendo de la pieza metálica impresa, para promover aún más la reutilización de materiales. Esta innovación en materia de sostenibilidad por sí sola puede suponer un enorme ahorro en costes de material.
Hace cuatro años, no podíamos prever todos los logros de ingeniería que se derivarían de nuestro trabajo como socio de IDAM, especialmente en un sector que evoluciona tan rápidamente como la fabricación aditiva. Sin embargo, las lecciones que hemos aprendido y los conocimientos que hemos compartido con otros líderes de la fabricación aditiva están resultando esenciales para impulsar el crecimiento de la impresión 3D como proceso viable en todo el mundo.
Puede ver nuestros últimos logros en RAPID + TCT y Formnext: el sistema de transferencia y recuperación de polvo metálico PowTReX y la estación de desempolvado automatizada DPS. Más información aquí.